Le monde d'après : Chapitre 5
Faire mieux avec moins, un retour aux sources du Lean ?
Antoine Perret | 2 juin 2020
Infographie
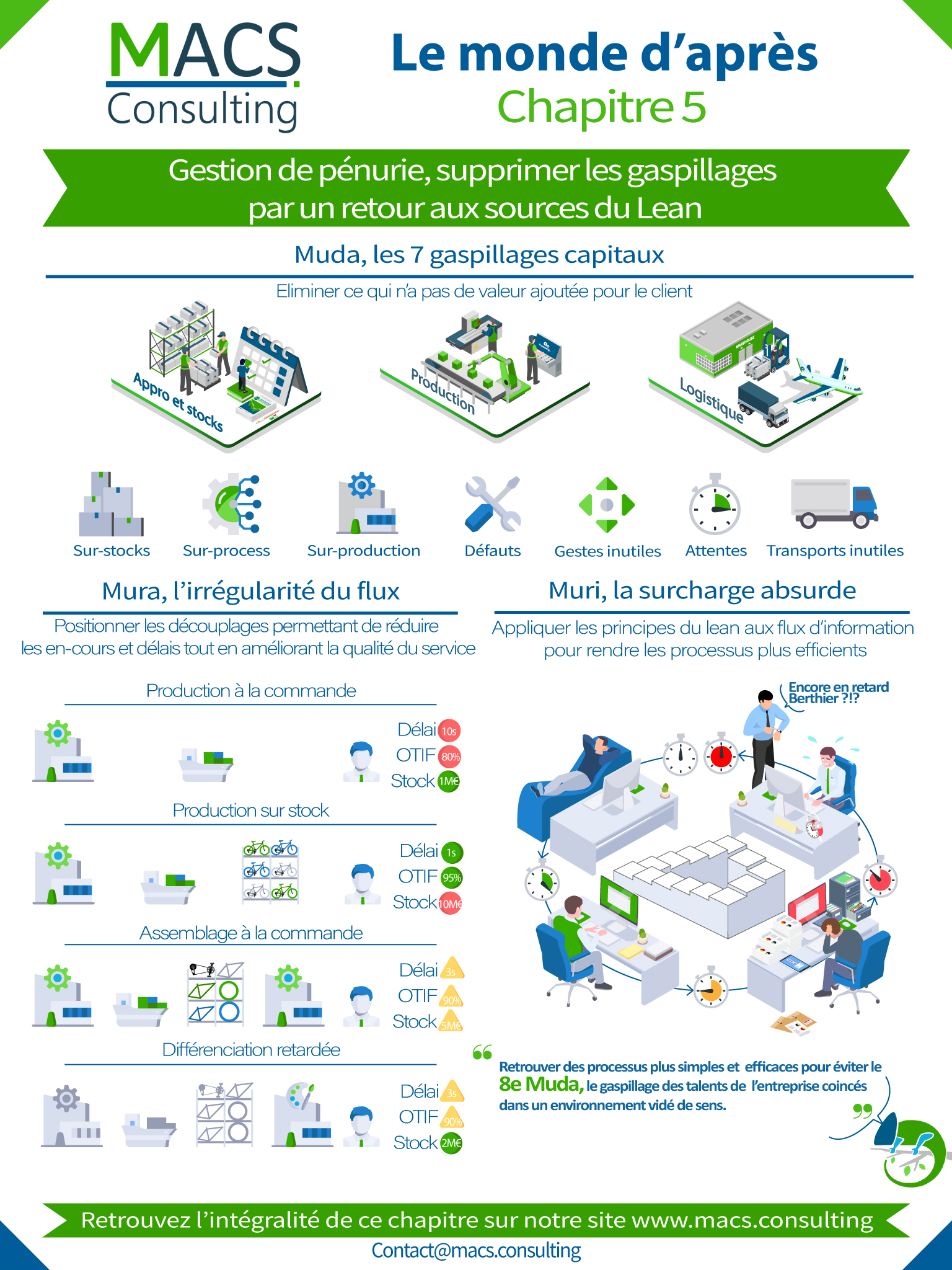
Muda, Mura, Muri
Ce n’est pas un hymne de gladiateur mais un rappel en japonais des problèmes à éliminer selon les principes du Lean Manufacturing.
A la sortie de la seconde guerre mondiale, le Japon doit reconstruire toute son industrie pour retrouver une part d’autonomie. Mais le pays dispose de peu de ressources, qu’il s’agisse d’énergie, de capitaux ou de matière première. C’est dans ce contexte de contraintes que le modèle de production de Toyota et par conséquent le Lean trouvent leur genèse.
A l’heure où les entreprises doivent remettre en cause leur fonctionnement pour des question sanitaires, économiques et environnementales, ces mots/maux résonnent avec toujours autant de pertinence.
Ce n’est pas un hymne de gladiateur mais un rappel en japonais des problèmes à éliminer selon les principes du Lean Manufacturing.
A la sortie de la seconde guerre mondiale, le Japon doit reconstruire toute son industrie pour retrouver une part d’autonomie. Mais le pays dispose de peu de ressources, qu’il s’agisse d’énergie, de capitaux ou de matière première. C’est dans ce contexte de contraintes que le modèle de production de Toyota et par conséquent le Lean trouvent leur genèse.
A l’heure où les entreprises doivent remettre en cause leur fonctionnement pour des question sanitaires, économiques et environnementales, ces mots/maux résonnent avec toujours autant de pertinence.
1. Muda, les 7 gaspillages capitaux
Surproduction, surstock, attente, transport, défauts, mouvements superflus et enfin étapes inutiles. Voici la liste classique des gaspillages à éliminer. Ils représentent ce qui coute en ressource à l’entreprise sans que le client n’y voie une valeur ajoutée.
En général, ils chassent en meute, les uns entrainant les autres. Un fournisseur lointain, ne sera pas très réactifs à cause du temps de transport, d’où le besoin de commander en avance qui nécessite de construire des prévisions détaillées. On rajoutera plus de stocks pour se protéger des variations de besoin ou d’un problème qualité car un renvoi pour retouche est inenvisageable. Enfin le stockage en masse à l’entrepôt génèrera des mouvements supplémentaires.
Ces actions sans valeurs ont pourtant un cout qui est in fine payé par quelqu’un : l’entreprise, ses fournisseurs ou ses clients.
Discussion ubuesque avec une contrôleuse de gestion dans l’aéronautique : « on ne peut pas réduire les temps de retouche car ils sont dans la gamme et on les refacture aux clients… »
En général, ils chassent en meute, les uns entrainant les autres. Un fournisseur lointain, ne sera pas très réactifs à cause du temps de transport, d’où le besoin de commander en avance qui nécessite de construire des prévisions détaillées. On rajoutera plus de stocks pour se protéger des variations de besoin ou d’un problème qualité car un renvoi pour retouche est inenvisageable. Enfin le stockage en masse à l’entrepôt génèrera des mouvements supplémentaires.
Ces actions sans valeurs ont pourtant un cout qui est in fine payé par quelqu’un : l’entreprise, ses fournisseurs ou ses clients.
Discussion ubuesque avec une contrôleuse de gestion dans l’aéronautique : « on ne peut pas réduire les temps de retouche car ils sont dans la gamme et on les refacture aux clients… »
2. Mura, l’irrégularité du flux
Un de fondamentaux du Lean est le travail sur le flux et sa régularité.
Une mauvaise compréhension a souvent associé Lean à zéro stock. Au contraire, le stock, à partir du moment où il est piloté, permet de protéger les activités de production de variations trop fortes de la demande. On parle alors de découplage. C’est un découplage en durée, car il permet de servir une partie des clients avec une délai court que ne permet pas la production à la commande. Également en priorité, car il laisse aux usines une fenêtre d’ordonnancement pour optimiser leurs productions.
Un objectif de la supply-chain est d’identifier, de dimensionner et de piloter ces stocks de découplage. Vient ensuite une approche Lean avec la production ou les fournisseurs afin de réduire les temps d’attente donc leur délai de réactivité (Lead-time). Le temps réel de production est régulièrement inférieur à 5% du délai annoncé. C’est encore moins sur les activités de contrôle, lorsqu’une relecture de 2 minutes peut attendre 1 semaine dans une panière. D’expérience, c’est là que sont les gains !
L’exemple des masques nous l’a montré, aucun stock ne peut couvrir tous les aléas pendant un temps long. Et avec l’obsolescence, on peut à la fois avoir payé cher pour le constituer et ne plus l’avoir disponible au moment voulu. Mais ils donnent le temps à la production pour se réorienter et faire varier sa capacité.
Une mauvaise compréhension a souvent associé Lean à zéro stock. Au contraire, le stock, à partir du moment où il est piloté, permet de protéger les activités de production de variations trop fortes de la demande. On parle alors de découplage. C’est un découplage en durée, car il permet de servir une partie des clients avec une délai court que ne permet pas la production à la commande. Également en priorité, car il laisse aux usines une fenêtre d’ordonnancement pour optimiser leurs productions.
Un objectif de la supply-chain est d’identifier, de dimensionner et de piloter ces stocks de découplage. Vient ensuite une approche Lean avec la production ou les fournisseurs afin de réduire les temps d’attente donc leur délai de réactivité (Lead-time). Le temps réel de production est régulièrement inférieur à 5% du délai annoncé. C’est encore moins sur les activités de contrôle, lorsqu’une relecture de 2 minutes peut attendre 1 semaine dans une panière. D’expérience, c’est là que sont les gains !
L’exemple des masques nous l’a montré, aucun stock ne peut couvrir tous les aléas pendant un temps long. Et avec l’obsolescence, on peut à la fois avoir payé cher pour le constituer et ne plus l’avoir disponible au moment voulu. Mais ils donnent le temps à la production pour se réorienter et faire varier sa capacité.
3. Muri, la surcharge absurde
C’est souvent la conséquence de Mura. Si l’on ne traite pas le problème des variations de charge et de délai, qu’elles viennent du client, du fournisseur ou de la chaine hiérarchique, on crée des pics de charge insolubles qui créent des tensions et usent les équipes. L’énergie sera ensuite mise à expliquer pourquoi on a été en retard. La réponse du Lean est de gammer le temps nécessaire: cela permet dans un premier cas de comprendre la difficulté réelle pour dans un second travailler à la réduire.
Et c’est là que sont les surprises, dans un sens comme dans l’autre. Si les équipes ADV sous sont l’eau, est-ce qu’il y a trop de commandes un jour par semaine ou bien que que le processus pour fournir un délai fiable au client est trop morcelé.
C’est le domaine du Lean Service, ou l’on simplifie et accélère les flux d’information avec un tri pour s’assurer de leur pertinence. Le potentiel est énorme, car derrière la généralisation des systèmes, on a noyé les utilisateurs sous une masse de données parfois contradictoires qui auto-génèrent du travail supplémentaire. Et la distanciation des équipes va amplifier les problèmes d’interprétation avec le risque que certains s’isolent et déconnectent.
Et c’est là que sont les surprises, dans un sens comme dans l’autre. Si les équipes ADV sous sont l’eau, est-ce qu’il y a trop de commandes un jour par semaine ou bien que que le processus pour fournir un délai fiable au client est trop morcelé.
C’est le domaine du Lean Service, ou l’on simplifie et accélère les flux d’information avec un tri pour s’assurer de leur pertinence. Le potentiel est énorme, car derrière la généralisation des systèmes, on a noyé les utilisateurs sous une masse de données parfois contradictoires qui auto-génèrent du travail supplémentaire. Et la distanciation des équipes va amplifier les problèmes d’interprétation avec le risque que certains s’isolent et déconnectent.
Il est temps de revoir les flux physiques et d’information avec vos équipes pour retrouver des processus plus simples et efficaces et éviter le 8e Muda:
le gaspillage des talents de l’entreprise qui partiront car ils se sentent coincés dans un environnement vidé de sens.
Accéder aux autres chapitres
Qui sommes nous
MACS est un cabinet de conseil spécialisé en Supply Chain, Performances des opérations et Conduite du changement. Si vous souhaitez révéler le potentiel de votre supply chain, contactez nous